How Roar Solutions can Save You Time, Stress, and Money.
How Roar Solutions can Save You Time, Stress, and Money.
Blog Article
The 5-Minute Rule for Roar Solutions
Table of ContentsRoar Solutions - The Facts5 Simple Techniques For Roar SolutionsRoar Solutions - Questions
In order to protect installments from a possible explosion a method of evaluating and classifying a possibly unsafe location is required. The purpose of this is to make certain the appropriate option and installation of equipment to eventually protect against an explosion and to ensure safety of life.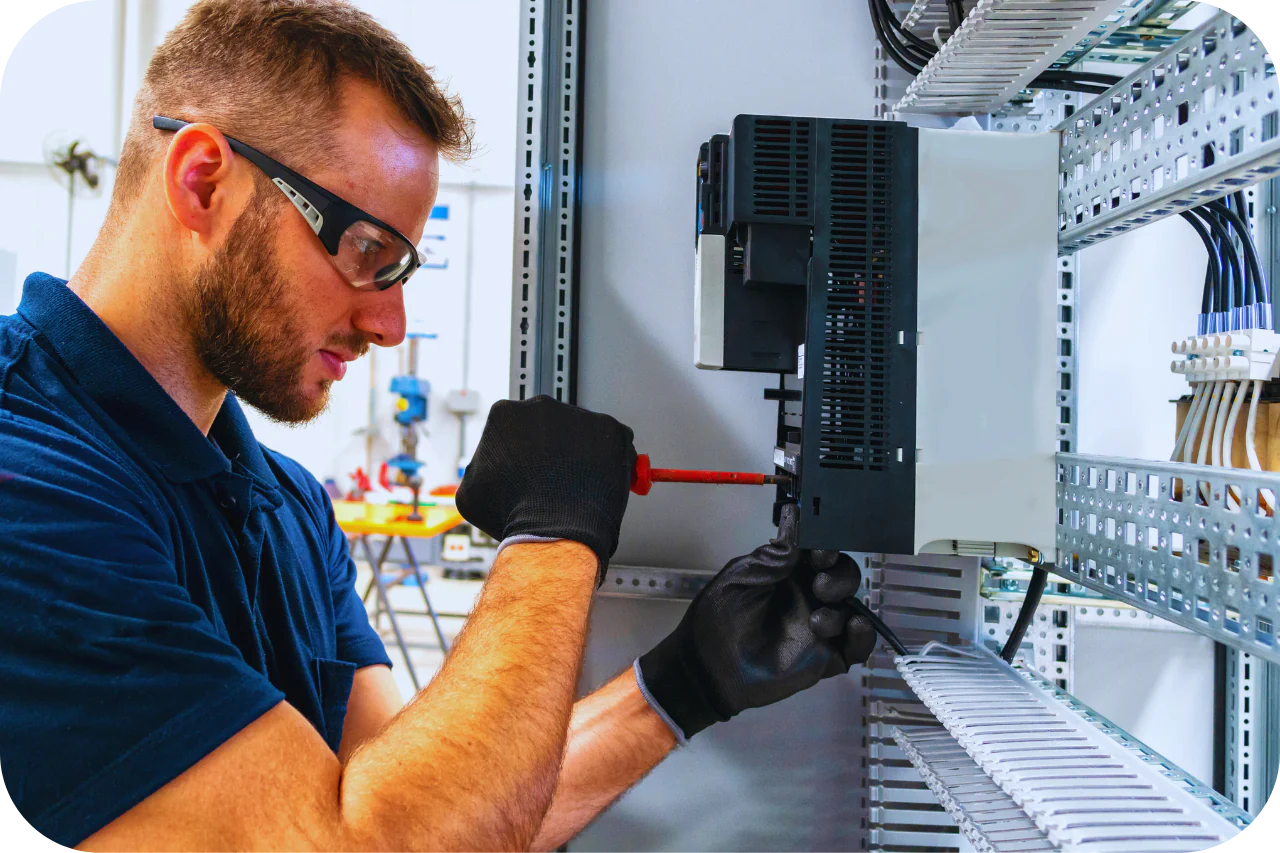
(https://experiment.com/users/roarsolutions)
No devices must be installed where the surface temperature level of the equipment is above the ignition temperature level of the given hazard. Below are some typical dirt unsafe and their minimal ignition temperature level. Coal Dust 380C 225C Polythene 420C (melts) Methyl Cellulose 420C 320C Starch 460C 435C Flour 490C 340C Sugar 490C 460C Grain Dirt 510C 300C Phenolic Material 530C > 450C Aluminium 590C > 450C PVC 700C > 450C Soot 810C 570C The chance of the hazard existing in a focus high sufficient to create an ignition will certainly differ from location to location.
In order to identify this risk an installment is divided right into locations of danger depending upon the quantity of time the unsafe is present. These areas are described as Areas. For gases and vapours and dusts and fibres there are three areas. Zone 0 Area 20 A harmful environment is very likely to be existing and might exist for long periods of time (> 1000 hours annually) and even continually Zone 1 Zone 21 A dangerous ambience is possible yet unlikely to be existing for lengthy durations of time (> 10 450 C [842 F] A classification of T6 indicates the minimum ignition temperature is > 85 C [185 F] Dangerous location electrical tools perhaps created for use in greater ambient temperature levels. This would certainly indicated on the score plate e.g. EExe II C T3 Ta + 60C( This suggests at 60C ambient T3 will not be exceeded) T1 T1, T2, T3, T4, T5, T6 T2 T2, T3, T4, T5, T6 T3 T3, T4, T5, T6 T4 T4, T5, T6 T5 T5, T6 T6 T6 A T Class score of T1 suggests the optimum surface area temperature created by the instrument at 40 C is 450 C. Assuming the associated T Course and Temperature level rating for the equipment are proper for the location, you can always use an instrument with a more strict Department rating than required for the area. There isn't a clear answer to this concern. It really does rely on the sort of equipment and what repairs need to be accomplished. Devices with specific examination treatments that can't be done in the field in order to achieve/maintain third celebration rating. Have to come back to the factory if it is before the tools's solution. Area Repair Work By Authorised Personnel: Complex screening might not be required however details treatments may require to be followed in order for the devices to preserve its 3rd party score. Authorised employees must be used to do the job properly Repair work have to be a like for like substitute. New component should be taken into consideration as a direct substitute needing no special testing of the tools after the repair is total. Each item of tools with an unsafe score should be reviewed separately. These are detailed at a high degree listed below, but also for more thorough info, please refer directly to the standards.
Roar Solutions - An Overview
The tools register is a comprehensive data source of devices records that consists of a minimum set of areas to recognize each product's area, technological specifications, Ex-spouse classification, age, and environmental data. This information is vital for monitoring and managing the equipment efficiently within unsafe locations. On the other hand, for periodic or RBI tasting examinations, the quality will be a combination of In-depth and Close examinations. The ratio of In-depth to Shut evaluations will certainly be identified by the Tools Risk, which is examined based on ignition threat (the likelihood of a source of ignition versus the probability of a combustible atmosphere )and the unsafe area category
( Zone 0, 1, or 2). This variant will certainly likewise affect the resourcing demands for job preparation. As soon as Whole lots are defined, you can establish tasting strategies based on the sample size of each Whole lot, which describes the number of random equipment products to be examined. To determine the called for sample dimension, 2 aspects need to be assessed: the size of the Whole lot and the category of inspection, which shows the level of effort that should be used( reduced, normal, or increased )to the assessment of the Whole lot. By incorporating the classification of assessment with the Lot dimension, you can then establish the proper rejection criteria for an example, implying the allowable variety of malfunctioning things found within that sample. For even more information on this process, please refer to the Energy Institute Guidelines. The IEC 60079 standard advises that the maximum period between inspections should not surpass three years. EEHA assessments will additionally be conducted outside of RBI campaigns as component of see this site set up upkeep and tools overhauls or repair services. These inspections can be credited towards the RBI example sizes within the impacted Lots. EEHA inspections are performed to determine mistakes in electric equipment. A heavy racking up system is vital, as a single item of equipment might have multiple faults, each with differing levels of ignition threat. If the combined rating of both assessments is less than twice the mistake score, the Lot is regarded appropriate. If the Great deal is still considered unacceptable, it has to go through a full examination or validation, which might set off more stringent examination protocols. Accepted Great deal: The sources of any mistakes are identified. If an usual failure mode is discovered, extra tools might need maintenance. Faults are classified by severity( Safety, Honesty, Home cleaning ), guaranteeing that immediate problems are analyzed and attended to quickly to mitigate any kind of effect on safety or procedures. The EEHA data source need to track and record the lifecycle of faults together with the rehabilitative activities taken. Executing a durable Risk-Based Evaluation( RBI )method is critical for making sure compliance and security in handling Electrical Equipment in Hazardous Locations( EEHA) (eeha training). Automated Mistake Rating and Lifecycle Management: Easily take care of faults and track their lifecycle to improve inspection accuracy. The intro of this support for risk-based inspection further enhances Inspectivity's position as a best-in-class option for governing conformity, as well as for any type of asset-centric inspection use case. If you want learning extra, we welcome you to ask for a demonstration and uncover how our solution can transform your EEHA administration processes.
How Roar Solutions can Save You Time, Stress, and Money.

In regards to eruptive danger, a hazardous area is an environment in which an explosive atmosphere is existing (or might be expected to be present) in quantities that call for unique safety measures for the construction, installation and use equipment. eeha courses. In this post we explore the obstacles encountered in the office, the risk control measures, and the needed proficiencies to work securely
It issues of modern life that we produce, keep or handle a series of gases or liquids that are deemed flammable, and a variety of dirts that are deemed combustible. These materials can, in certain problems, form explosive environments and these can have significant and unfortunate effects. Most of us recognize with the fire triangle eliminate any one of the 3 aspects and the fire can not happen, but what does this mean in the context of hazardous areas? When breaking this down into its most basic terms it is basically: a combination of a specific quantity of release or leakage of a certain substance or material, blending with ambient oxygen, and the existence of a resource of ignition.
In the majority of circumstances, we can do little about the levels of oxygen airborne, however we can have considerable influence on resources of ignition, for instance electric tools. Unsafe locations are documented on the hazardous location category illustration and are identified on-site by the triangular "EX" sign. Here, among other crucial information, zones are divided into three kinds relying on the risk, the likelihood and duration that an explosive environment will certainly exist; Zone 0 or 20 is considered the most unsafe and Zone 2 or 22 is regarded the least.
Report this page